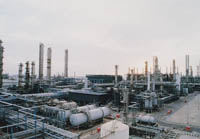
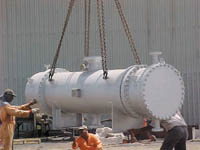
UAE-based Serck Services (Gulf) Ltd is established as a leading manufacturer of shell and tube heat exchangers for the Middle East's growing oil and gas industry.
From petrochemical plants to power stations, leading industries continue to depend upon Serck's high quality products, unrivalled expertise and vast experience to meet their exacting demands.
Through ongoing expansion, the company has upgraded its Sharjah manufacturing facilities, which now utilise the latest technologies and quality standards including DNV ISO9002 accreditation, the only such heat transfer company in the Middle East to have achieved this.
Included at the plant is a fully-equipped mobile workshop and specialist refinery shutdown team, ASME IX coded welders, a 24-hour emergency repair facility and riding squads for marine repairs, a specialist heat exchanger cleaning facility using HP washing machines, hydrobrush shooting and water drilling equipment. Vibrasonic cleaning of air coolers and heat exchangers is also carried out at the plant.
Serck provides a wide range of heat exchanger services, including condenser manufacture, retubing and restoration, condenser cleaning, eddy current tube testing, and the manufacture and retubing of air coolers.
Condenser manufacture: Serck Services designs and manufactures new heat exchanger units at its Sharjah workshop to client specifications
Condenser retubing: Serck is synonymous with the retubing of units on board or on-site for companies both Gulf-wide and worldwide
Condenser restoration: A thin walled metal shield made of highly durable alloys repairs both tube end erosion, restores the tube to tube-sheet integrity and restores leaking or plugged tubes to full operation. Complementing this service is Serck Services' 100 per cent solid epoxy coating for tube sheets, whereby tubes are totally plugged for grit blasting, with the coating applied under controlled temperature and humidity conditions. The coating is said to be ideal for combating abrasion, corrosion and galvanic reaction.
Condenser cleaning: Portable 5,000 and 10,000 psi machines provide high pressure washing for all kinds of tube cleaning, while specialist water drilling equipment is used on totally blocked tubes. Serck also offers brush shooting, whereby nylon brushes are shot through the tubes using a combination air/water gun to effectively remove mud, slime, silt, barnacles and algae. Finally, chemical cleaning and descaling is offered on board vessels or in the workshop.
Eddy current tube testing: A tube leak in a heat exchanger can be costly in terms of unscheduled downtime, major equipment repairs and/or unit contamination. An eddy current analysis detects, identifies and locates potential tube failures before they become leaks. This improved detection and evaluation of tube defects means better protection for equipment.
Air cooler manufacture and retubing: Serck Services offers specially designed fin blocks which offer excellent heat exchange and pressure drop characteristics. The round tubes are easily cleaned and fins are available in copper or aluminium. In addition, aluminium-finned aluminium brass tubes manufactured by Serck gives an immediate solution to air cooler problems.
The latest in a long line of contracts, 13 of Serck Services' heat exchangers have most recently been supplied for a refinery in Chad, a project which included data calculations and mechanical design.
Today, Serck's range of products and services are offered through a network of branches throughout the Gulf states, which complement the company's extensive UK, US and Continental Europe network. The Sharjah facility is currently applying for the ASME 'U' stamp, according to the company. In addition to heat exchangers, the company also produces radiator elements and air conditioning coils at Sharjah.
Serck Services (Gulf) Ltd is a wholly-owned subsidiary of UK-based Partco International.