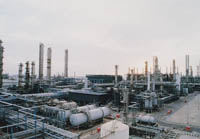
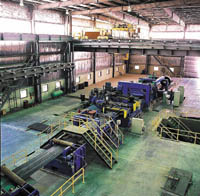
Saudi Steel Pipe Company Ltd (SSP) recently announced that it had successfully passed its API 5L and ISO9002 audits, which puts it squarely in the contest for the many pipeline projects which are springing up around the Middle East.
With much hard work and the cooperative support of many of the operating divisions of Saudi Aramco, the company is now one of but a few qualified suppliers to Aramco's recently-modified specification for liquid hydrocarbon flow lines, SAMSS 332.
To meet the requirement of this new specification, SSP had to pull out all the stops in introducing the latest available technologies on the market for putting its state-of-the-art High Frequency Induction (HFI) welded steel pipe plant together.
This new plant, which started commercial production in August last year in Dammam's Second Industrial City, is the newest such mill in the world and features coil joining and a 200 tonne accumulator which will allow the mill, once sized in to the target specification, to run continuously, thereby avoiding any quality problems which might result from traditional single-coil feed mills.
The introduction of a Linsinger strip edge milling system combined with an advanced linear forming operation brings the pre-welded pipe to the induction coil in as clean and consistent a manner as is possible, thus allowing for predictable welder performance. A last critical operation is the post weld annealing of the pipe utilising a two-electrode system from AEG Elotherm. This system is equipped with seam tracking which ensures that the normalisation of the heat-affected zone is always centred on the bond line.
There are two very unique computer operating systems at work in SSP's new mill; namely, a sophisticated tube tracking system which builds a history on each length of pipe from the time the coiled strip enters the operation until the finished pipe exits the building for shipment. This element of traceability is growing more critical in the marketplace as concerns for product liability and product safety are on everyone's mind.
The second computer system at work for SSP is the Continuous Electronic Process Control (CEPC) system which was introduced to bring SSP into compliance with Saudi Aramco's new specification.
This system is at the heart of SSP's welding operation and provides real-time monitoring and recording of all the critical welding variables which affect welder performance.
The system is tied into an elaborate metallographic regimen for evaluation of metal flow angles in the weld area. This process of testing and measuring upset angles is conducted throughout the production cycle.
SSP has been recognised as the premier manufacturer of welded steel pipe in the Kingdom since 1980 when it first started production of 12" to 4" black and galvanised welded steel pipe to ASTM, BS, ANSI and Saso standards. This new plant for the manufacture of 6" to 16" welded steel pipe to API 5L and related industry specifications only assures SSP's position in the marketplace as the company which sets a new standard in product reliability.
The company is also proud to announce that it has now successfully manufactured its first API 5L X42 10" 70km pipeline project to Dove Energy, which is operating in Yemen.
Furthermore, there are several other projects on the cards, with others in tender.
SSP is an industrial joint venture between Saudi entrepreneurs Rabiah & Nassar Company, Al Khorayef Sons and Fahad Moh'd Al Saja and Shinho Steel Company of South Korea.
For further information, visit www.sspipe.com