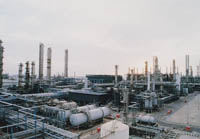

Arabian Pipes Company (APC) is currently nearing completion of another stage of its continuous development to maintain its position as the leading Electric Resistance Welding (ERW) pipe manufacturer in the Kingdom, and to strengthen its position within the Middle East and Asia.
The 6" to 20" ERW mill based in Riyadh, Saudi Arabia has been operating since 1996 and has an annual capacity of 184,000 metric tons.
The joint stock company has recently invested more than $6 million to provide new equipment to replace and enhance the current facilities.
Its aim has been to target productivity and quality improvements which will give optimum benefits to customers throughout the region, in terms of price and quality, and ensure that they meet the most demanding specifications of customers worldwide in order to continue to develop the export market.
The developments follow on from recent improvements at APC, which have seen it become the first ERW manufacturer to be qualified and approved to the new Saudi Aramco specifications.
Strip Edge Milling Machine
Ordered in July 2000 the BKB 1100-1650 machine was manufactured in Germany by SMS Meer and is the largest machine of its type available. Operation is at speeds of up to 100 feet per minute and covers the full range of APC products from 6" to 20" diameter, 3.2mm to 16mm wall thickness in grades up to X70.
The machine is equipped with two 1100mm diameter milling heads with 74 carbide inserts per head, each driven by 170kW AC speed-controlled motors which automatically control the rotational speed based on the Strip Line Speed.
The fully-automated machine is equipped with state-of-the-art CNC and PLC control and all axes have digital measuring systems with accuracy of 0.001mm to provide the exact finished strip width for forming and welding.
The Edge Milling machine, which replaces the Edge Shearing method previously employed, provides the cleanest, squarest strip edges possible and guarantees optimum quality edges as required by the most demanding of line pipe specifications for the High Frequency Welding process.
Seam Annealer
APC has installed a fourth in-line 1kHz Induction heater supplied by Ajax Magnathermic (UK) which has a capacity of 500kW and increases the companyÕs total seam heat treatment capacity to 2000kW. The unit is equipped with automatic temperature control and automatic seam following system and complements the Continuous Electronic Process Control system already employed at APC.
The additional heating power will allow APC to both increase manufacturing speeds (productivity) and ensure that the weld heat affected zone (HAZ) is fully normalised (quality).
The improved metallurgical structure due to the additional heating ensures that even on products with high wall thickness the weld seam is homogeneous with the base metal.
The resulting weld area has consistent through-hardness, reduced grain size and improved impact results and meets
the most stringent testing requirements employed for quality line pipe.
Ultrasonic Machines
APC has recently upgraded its automatic Ultrasonic Inspection systems with the assistance of its long-term supplier and the world leader in this field, Krautkramer (Germany), to bring the ultrasonic testing equipment to the highest standard available.
All machines are equipped with automatic alarms, paint sprays and recording facilities and APC carries out static and dynamic calibration to the most stringent standards.
The Full-Body Ultrasonic Testing Machine has been upgraded both electronically and mechanically and now employs the Krautkramer USIP20 GP8 multi-channel flaw detector that can be fitted with up to eight 4-6MHz straight beam probes for detection of laminar defects in the pipe body.
The On-Line Ultrasonic Testing Machine, which also employs the Krautkramer USIP20 GP8, has recently been modified to incorporate two large straight beam probes to test the area adjacent to the weld seam.
This test provides 100 per cent inspection for laminar defects in the strip edges as required for the most demanding service.
Marking Machines
APC has recently installed
and commissioned two automatic Paint Marking machines supplied by Numtech Interstahl (Austria). Both machines have been installed to improve productivity and product traceability; they
are both PC- based and
interface directly with the APC Manufacturing Information System (MIS) to transfer pipe
data and with the automatic pipe length and weight measurement system.
The Dot Paint Marking Machine (DP) is a computer controlled two-axis manipulator that is used to identify the pipe with its unique number immediately after it is cut from the coil. The number is positioned at 90 degrees to the weld and is then used for identification throughout the process.
The Paint Jet Machine (PJ) utilises a state-of-the-art fully-automated multi-axis industrial robot machine to mark the Customer Information (Stencil) on each pipe. The machine can perform both inside and outside surface marking and can mark up to 10 lines of information within 45 seconds.
All of the developments have been wholly managed and controlled by the highly qualified and experienced Engineering and Technical staff at APC.
Further significant investment is already planned and approved and will be carried out in controlled stages over the next four
years.
It is the aim of APC to meet
and exceed the demands
of its customers and this process
of Continuous Development
is a strategy that APC knows
will maintain, and will further develop its position and reputation as a world-class ERW pipe manufacturer.