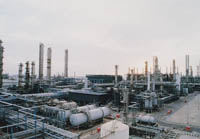

Rigid application of quality control is a feature of every step of the APC process.
Products of the highest quality are fundamental to APC's operations, as certificates from the American Petroleum Institute (API) and ISO9001 can testify. The company's Riyadh ERW mill utilises the latest test and inspection facilities, thanks to key recent investments in a fourth in-line induction heater for stringent testing of quality line pipe and an upgrade of automatic Ultrasonic Inspection systems.
Providing customers with a quick, efficient service response, APC operates a strict company-wide total Quality Assurance Programme.
This programme is implemented from initial procurement of the raw material through the processing phase and up to final shipment of the goods.
Under such a programme, APC is able to ensure that all delivered products can be used with confidence.
The companyÕs Quality Control section ensures that the straightness of the pipes, end-facing and all other aspects of pipe manufacture are within specified and acceptable international tolerances.
The principal inspection and tests undertaken by the Quality Control section of the company include chemical and physical analysis; tensile strength testing; dimensional inspection; ultrasonic inspection; hydrostatic testing; deformity testing and hardness testing.
During production, great attention is placed by the company on the quality of the weld area. The pipe weld area is seam-annealed after welding to enable the same microstructure of the steel as the parent metal.
To maintain a strong, sound weld strength, non-destructive tests and inspections are performed during and after the welding process.
Frequent physical tests are also applied after welding to determine overall pipe resilience. Equal emphasis is also placed on other aspects of pipe testing and inspection.