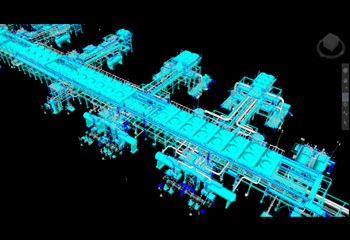
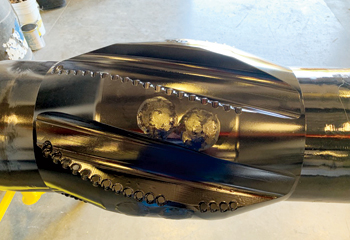
As modern drilling methods have created new wear problems for the drill string and drilling tools, several cost saving products and applications have been developed to protect it, Colin Duff, Global Director of Hardbanding Solutions by Postle, tells OGN
Drilling methods today are unrecognisable in comparison with the simple vertical wells first used to reach hydrocarbons in the past. The industry has evolved to become more efficient through the decades, and can now discover previously inaccessible fields.
'An industry pushing the boundaries of directional and faster drilling, aided by new and emerging technology, has led us to where we are today. However, these methods demand more from the drill string, and so new products and procedures have been developed to prevent failure caused by wear during drilling operations,' says Colin Duff, Global Director of Hardbanding Solutions by Postle.
DRILL PIPE HARDBANDING
The most common wear protection technology used is ‘drill pipe hardbanding’. The materials applied, such as Duraband® NC, have been designed to give maximum protection to the tool joint as it encounters abrasive and impact wear from both the casing and open hole during drilling.
![]() |
Typical tool joint hardbanding |
Hardbanding is typically applied in 3 x 1-inch bands on the drill pipe box tool joint. It can also be applied on HWDP and drill collars. The rate and amount of wear on the sacrificial hardband varies widely depending on several factors including formation and well profile.
There are a range of hardbanding products available. And it is vital that pipe owners as well as oil and gas energy companies are involved in the decision regarding the choice of hardbanding used.
They should demand a material with three properties, which when applied to the correct procedure, result in the most effective protection:
• Resistance to severe abrasion and impact, for maximum life between reapplications.
• A low friction factor against casing to protect the casing when rotated against it.
• A crack-free and defect-free application allowing for simple re-application when worn, without the need for removal, minimising repair costs.
When the correct hardbanding is applied to drill pipe, HWDP and drill collars, it provides the drill string with cost-effective protection, greatly extending its working life.
NON-MAGNETIC HARDBANDING
![]() |
Non-magnetic Ultraband NM with cast tungsten |
Non-magnetic drill collars and related components are fewer in volume than drill pipe, but each tool carries a significant capital expense.
Wear is common, and several methods have been adopted to prevent it. Regular hardbanding materials cannot be used as they are magnetic and interfere with the measurement-while-drilling (MWD) equipment.
Plasma transfer arc (PTA) applications have been used but the equipment is not widely available and is expensive.
Simple stainless steel welding wires like 310 have been applied but they don’t provide sufficient abrasion resistance.
More advanced non-magnetic hardbanding products have now been developed, like Ultraband NM from Hardbanding Solutions. This material stays below maximum permeability requirements and will wear 4-5 times longer than 310. It is 100 per cent crack free and can be reapplied when needed for continued protection of these expensive assets. It’s also possible to add cast tungsten carbide to the weld for even longer protection.
TOOL JOINT REPAIR & BUILD-UP
Some hardbanding materials on the market stress crack and must be removed before reapplication. When this is done, typically by industrial grinding or plasma, a recess is left in the tool joint. This must be repaired before a new hardbanding can be applied, and there are welding materials, such as tool joint build up (TJBU) to achieve this. The same material can also be used to build-up the outer diameter of a worn tool joint.
![]() |
Repair with TJBU after plasma removal |
MUD RING EROSION REPAIR
Erosion caused by drilling mud or air drilling can be common in some drilling regions, particularly where faster drilling methods are used. The tool joint wears from the 18-degree taper. Previously this was a case for rejection of the drill pipe.
Hardbanding Solutions has now developed a procedure using TJBU wire, which matches the original tool joint hardness and brings the tool joint back to its original geometry.
![]() |
Mud ring erosion |
SPIRALBANDING
![]() |
Spiralbanding ... protection of the drill pipe body |
Launched in 2021, spiralbanding is a new application technology for the protection of the drill pipe body.
Damage and wear are found in the centre of the drill pipe when used in lateral sections of the well. The pipe deflects or buckles, forcing this area against the open hole.
Until now there was no effective solution because standard hardbanding could not be applied to the thinner wall of the pipe body (in comparison to the tool joint, which has a much greater wall thickness).
Advancements in welding technology, combined with a new wire and procedure, have made effective protection possible. In some cases, spiralbanding has extended the life of drill pipe in the lateral by three times
COMPLETION TUBING BUILD-UP & HARDBANDING
Hardbanding Solutions, using its experience with drill pipe, created products and procedures designed for both build-up and hardbanding of completion tubing (also known as work-string tubing).
This has revolutionised the use of these tools in the US and they are now commonly repaired and protected with TubeWeld 110 and Duraband NC wires respectively.
![]() |
Completion tubing with Duraband NC |
COMPLETION TUBING SLIP CUT REPAIRS
Slips can damage completion tubing by leaving deep scores in the outer diameter. These scores can be deep enough to cause the connection to be rejected during inspection.
A new repair procedure has been developed using new welding technology coupled with TubeWeld 110 wire.
![]() |
Slip cut damage |
STABILISERS
Stabilisers have been protected with hardfacing for many years. The ‘blades’ of the tool are traditionally hardfaced using tungsten carbide tiles or similar wear prevention technology with welding powders.
More recently, Hardbanding Solutions introduced the PS-11 tungsten carbide MIG wire for easier application and reapplication.
![]() |
Stabilizer protected with PS-11 |
DRILL-N-REAM TOOLS
![]() |
Duraband Domes on the Drill 'N' Ream Tool |
One of the more unusual wear solutions recently developed is the Drill-N-Ream® (DNR) tool developed by Superior Drilling Products (SDPI) from Vernal, Utah (US).
The procedure developed involves welding wear pads in the critical areas of the tool with Duraband NC, nicknamed ‘Duraband Domes’.
They protect the casing and the Polycrystalline Diamond Compact (PDC) cutters on the Drill-n-Ream (DNR) tool when it is rotating within the cased region of the wellbore.
Service companies in every drilling region are now offering a wider range of these wear prevention technologies wherever they are needed.
A combination of different hardfacing products and procedures, used correctly wherever they are required, can greatly extend the life of the drill string, even in the most challenging drilling conditions.
The result is that drill string owners can adopt the most modern drilling methods and still save significant costs by protecting their assets.