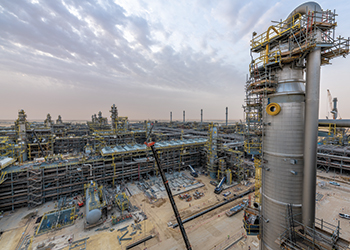
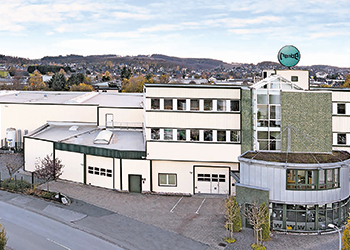
As technology moves forward with new manufacturing techniques, the need for proper plant protection has increased, and REMBE has a full range of state-of-the-art devices and solutions to protect the plants
As the demand for production across various industries increases, so does the need for proper protection of plants, which are replete with high pressure and critical equipment; inadequate plans and systems can lead to loss of life and property.
REMBE, a key player in the field of pressure relief and explosion safety, realises the risks and has been protecting the industry for the last over 45 years through innovative products.
The German company provides overpressure and vacuum protection solutions for customers in the oil, gas and petrochemical industries as well as protection concepts for those industries that may experience explosions due to combustible dusts.
Commenting on the situation, Orhan Karagöz, Chief Business Development Officer Process Safety, REMBE, says: "As technology moves forward with new manufacturing techniques, REMBE has developed a full range of state-of-the-art devices and solutions to protect the plants. The need for more production means that the demand for proper protection must be designed into the plant from the start.
![]() |
Orhan Karagöz, Chief Business Development Officer Process Safety, REMBE |
He says where existing plants are upgraded or expanded, REMBE can work with the client to ensure that the correct safety concept is in place.
According to him, in general, there is a lack of understanding of the need to really protect plants from overpressure and/or vacuum. "The current thinking of reliance on control or instrumentation for protection is flawed. Only a failsafe device like REMBE rupture discs will ensure that no matter what, the relief of the excess pressure happens when the control systems fail or a runaway reaction occurs," he remarks.
He says the REMBE devices are fully open in milliseconds. "No valve can match this speed or reliability and this is available 24/7 with no need for any outside control or activation system, the pressure does the work," he adds.
Karagöz continues: "Rupture discs and the Elevent Breather Valve cover all unplanned excessive pressure situations that will always be available as failsafe devices that operate within strict specifications to protect the industry. Meanwhile a range of explosion protection devices protect manufacturing facilities from combustible dust explosions."
Meanwhile James Hay, Managing Director REMBE GmbH Safety + Control (DMCC Branch), says there have been many cases where REMBE rupture discs that have protected a plant from disaster.
![]() |
James Hay, Managing Director REMBE GmbH Safety + Control (DMCC Branch) |
"In one case, a petrochemical plant lost all power during a production run and the chemical reaction caused a fast and uncontrolled pressure rise. The only safety equipment that functioned were the REMBE rupture discs that relieved the increasing pressure and protected the reactors from being destroyed, thereby saving the plant and possibly lives," he says.
Over the last 45 years, REMBE has constantly developed new products using its own engineering and R&D facilities in Germany to keep ahead of various industries or in partnership with clients to give them a solution to a problem they have.
Recently, it had the need to provide a fast and advanced solution for a client that needed over 20,000 rupture discs a year. "This involved new engineering, tooling and machines to put in place a REMBE solution in record time with 100 per cent satisfaction for this client," the spokesman says.
REMBE solutions are tailor-made to suit the operating conditions of the application. The company works with the client to ensure they get the best safety concept for their plants. This can be a range of different products for each application. "It is a team effort, both in REMBE and with the clients, to match safety to the application," says Hay.
![]() |
REMBE signalling device |
Commenting on business these days, where both oil prices and the pandemic has posed challenges to companies around the world, he says: "Obviously, the lower oil prices and the Covid-19 situation pushes us to keep reinventing ourselves. But we are well within our ability to meet any challenge."
Nevertheless, REMBE continues to grow and develop. It has built new premises and additional manufacturing facilities and is currently upgrading its existing main facilities to cope with the increased business.
"We are a company that is headquartered in Germany and we only manufacture in Germany. But we are an international company with offices all around the world. We have built up our business to cover the world while still remaining a family business with the interaction that allows. This means we can respond faster and more efficiently than much larger organisations. A personal touch is core to our business," says Hay.
For REMBE, the Middle East has been a major focal point. It offers full support to the region through its Dubai office. The company realises the importance of local support with an experienced staff that has knowledge of local needs.
"The team dedicated to looking after the Middle East is expanding to suit the workload and we have always put the client first with full support in place over many years. We offer sales and technical support as and when needed," says James Hay.
![]() |
REMBE rupture disc |
REMBE has prudently tackled the Covid-19 situation. Its facility in Germany and offices around the world are Covid-19 safe and it had developed its own protection plan long before the government had it in place.
"Our CEO together with the senior management team has implemented a concept and have been one step ahead of the situation all along. Our focus is on protecting our staff and the production of all our products to be able to offer protection products to our client’s plants as usual," says Karagöz.
All this has allowed REMBE to remain fully operational in terms of production. Its office-based staff is available working from home except for those positions that can only be done in the office. And even for the latter staff, the company has ensured enough space for absolute safe distancing in place, full cleaning and protection regimes.
To keep stakeholders in the industry abreast of the latest in the field of safety, REMBE organises its annual Process Safety Days and Explosion Safety Days. And with the current pandemic situation, the company has developed an online program for both process and explosion safety webinars using Zoom.
![]() |
A combination of rupture disc and safety valve |
"The customer response has been overwhelming! These webinars help us reach the key people in a multitude of industries. We alternate between pressure and explosion topics with input from our experts to open up their knowledge as well as be able to interact and answer questions that come up," says Karagöz.
"This is another innovation that again proves our response to any situation and is in place rapidly and for all customers as needed, just like our products. You can rely on REMBE 24/7," he concludes.