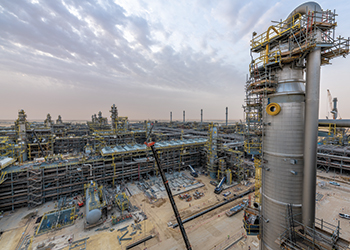

A multiphase flow meter on every well allows to understand the moment-by-moment dynamics of not only individual wells, but also the interactions between wells within their fields
Multiphase flow meters (MPFMs) are a strategic investment in optimising an oil field’s production flows, resulting in saved costs, increased profits, and streamlined operations. However, traditional multiphase flow meters are notoriously unable to handle continuous operation at every well head.
Crude oil comes out of the ground at varying pressure extremes, which is just one factor of many that contributes to the difficulty of obtaining accurate multiphase flow measurements. Many MPFMs are developed in controlled lab conditions that result in low accuracy and narrow operating ranges when applied in the field.
One way to increase accuracy is to use radioactive gamma-ray MPFMs. However, their high setup costs, size, high energy usage, and the constant security concern regarding the nuclear radiation sources results in radioactive MPFMs being inadequate applications to multi-well fields.
Additionally, the costs associated with the maintenance of machinery used in oil and gas production are extremely high. With the goal of reducing costs, many users purchase flow meters that work by physically separating the oil, water, and gas that is present in crude oil. However, they have high hidden maintenance costs that often go overlooked.
The extra piping required for these meters also poses an issue. Due to their bulky size and high demand for manpower to manage the equipment, this method of flow measurement makes monitoring every well simultaneously unfeasible. Regular maintenance is required to keep the separators clean of sand and other debris, which is another contributing factor to high maintenance costs and low levels of accuracy.
While the use of MPFMs in oil and gas applications has traditionally been filled with these aforementioned challenges, the benefits that can be gained by knowing every well’s performance in real-time are too great to ignore. The right MPFM has the power to increase a company’s automation level and raise its productivity.
At the forefront of the oil and gas industry’s digital transformation, Brown Hawk Technologies has developed a non-radioactive MPFM that provides users with continuous, accurate multiphase flow data at every well head in the field simultaneously.
The Brown Hawk Multiphase Flow Meter (BH-MPFM) does not employ radioactive technology, physical separation, infrared, or venturi methods, which have traditionally posed problems for many users. Rather, the BH-MPFM utilises a new patented technology, drawing from the company’s history in aerospace and defence.
Similar to radar tracking technology used in missile targeting, the sensor suite in the hardware detects the unique energy signatures created by the gas and fluid as crude oil passes through the device. The BH-MPFM locks onto and tracks these unique signatures to calculate the oil, water, and gas measurements simultaneously at 40 samples per second.
Telling OGN, Chris Brown, Founder and Chief Technology Officer at Brown Hawk Technologies, explains: "One major advantage to having multiphase flow meters on every well is that the user is able to truly understand the moment-by-moment dynamics of not only individual wells, but also the interactions between wells within their fields."
By using data analytics in combination with hardware data collection, the BH-MPFM allows for full oil field automation. Rather than using costly and labour-intensive activities to monitor the multiphase flow of each well, the BH-MPFM automatically and remotely captures flow data, which is then analysed in real time to give constant, accurate insight into every well’s performance. The BH-MPFM also allows for digitally predicting the required maintenance for other equipment used during oil and gas production. Brown explains: "The BH-MPFM’s own maintenance requirements are virtually nonexistent. However, if a problem is detected, the operator will know in less than a quarter of a second."
Not only is digital maintenance a key solution for an age-old problem, but it also significantly reduces costs while introducing a new industry standard. For oil and gas companies, greenhouse gas monitoring is another strategic investment that improves operational efficiencies and enables cost-effective mitigation plans. Brown Hawk provides an efficient and cost-effective method of monitoring gas emissions at every well, which allows producers to capture this valuable gas before it can escape further down the line.
Furthermore, the energy requirements for the device itself are minimal. The BH-MPFM consumes less than 5 W of energy and can also be operated solely through solar power. Adding a small solar panel generates plenty of power to run continuously and to keep the batteries charged for over 48 hours under no-light conditions.
The oil and gas industry’s shift towards automation, digital maintenance, and emissions mitigation have resulted in seemingly small concerns becoming urgent current issues that must be addressed with any strategic technological investment. Companies now need to innovate not only to remain competitive, but also to survive.
As the industry incorporates new best practices amidst this changing landscape, consideration of these factors will play a crucial role in determining the best investment for the user’s needs in multiphase flow monitoring.