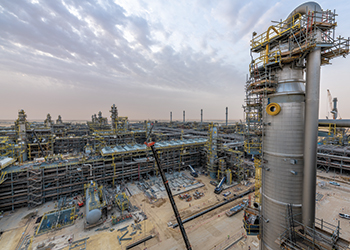
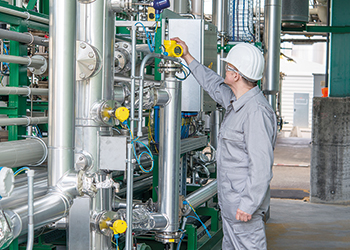
Despite the limitations of traditional technologies for interface level measurement, their great importance make them hard to replace, Alexander Alexis, Product Manager, VEGA Technique – Middle East office, tells OGN
The separation process in the oil and gas industry occurs at different levels. From the moment crude oil is extracted from the ground, the amount of water entrained with the precious crude has to be measured, both for accounting it off as well as for control.
With the current market demand to have more profitability by optimising operations and reducing loss, the need to accurately separate out the crude from water has been highlighted with importance.
Several measurable techniques have been deployed since the early automation times. Once the crude is extracted, different stages of separation happens in separators, desalters, dehydrators, preheaters, production traps and the list goes on.
![]() |
Interface level measurement in the dewatering tank |
Interface level instruments based on measurements inferred from basic variables like pressure, buoyant force and capacitance were and are still used to find out where the water level would be. These traditional technologies had inaccuracies of their own, but the availability of these measurement were of great importance which make them hard to replace.
In recent times, accuracy of interface level measurement instruments have been scrutinised more to achieve better control of the separation process. Newer technologies like the guided wave radars have been hence employed to improve this.
Before we elaborate further, let’s discuss the limitations why older technologies like displacers and pressure transmitters, which are still reliable, couldn’t add on to further process improvements.
HISTORIC MEASUREMENT METHODS
![]() |
Multiple-Point Density Array installed on a separator |
The first set of instruments used for interface level measurement were differential pressure, displacer and capacitance level transmitters. All of them were introduced into the market to measure level in a tank; but they could easily be calibrated for measure interface level as well.
For level measurement, these instruments were calibrated to measure a change in variable, like pressure or dielectric, with respect to a gas layer on top. So an empty vessel would be considered as a zero percentage and a tank full of product will be calibrated as the hundred percentage. Once set, a response between the calibrated range will be linearly converted into level.
Interface level measurement is no different. Unlike measuring the level, instead of calibrating with an upper gas phase, interface is calibrated with the upper fluid full in the vessel. So a variation in the lower phase with the vessel full of the upper liquid, is linearly inferred as the interface level. From the way how we have described the calibration, we can also judge the limitation of this method of measurement.
Apart from the level, density is one parameter which can vary considerably based on the type of crude oil, temperature and pressure. This variation can be inferred incorrectly as an interface level. Additionally, if the upper liquid drops below the calibrated range, the calculated values will be incorrect.
In such measurements the upper layer has to be maintained above the hundred percentage for the measurement to work.
To make sure that the interface level measurement functions well the operations, process and design teams should work hand-in-hand to select and operate within a desired range, suiting both the process and the instrument as well.
For instance, if the tapping points of the level transmitter’s bypass chamber is placed too high in a crude oil separator, the chamber will never be filled with the oil.
Likewise if the instruments are installed directly inside the vessel, then the measuring ranges should be selected where the oil level is operated above the top of the measuring range.
MODERN DAY INSTRUMENTATION
A benefit in using guided wave radar level transmitter technology is the capability to measure interface irrespective of the level of oil. The measurement philosophy is entirely different compared to inferred measurement.
A differential pressure transmitter will measure the change in hydrostatic pressure between oil and water. This is based on the assumption that the density of the two fluids is known and doesn’t change.
Displacer level transmitters work on the same philosophy, except that they measure the buoyant force with a mechanical float arrangement.
In both cases, change in density of the process fluid creates major inaccuracies. A guided wave radar measures the top of the oil and water interface by measuring the time taken for microwaves to be reflected off the oil and water surface.
Any process parameter will not impact or create inaccuracy in the reading. The dielectric constant would be the only limiting factor but since it varies slightly between different crudes, it doesn’t pose much issues in terms of inaccuracies.
Nevertheless, guided wave radars still can face issues due to poor reflections from emulsions that can form inside the process. Since there is no definite interface layer anymore, a poor or no-reflection can create reliability issues and will cause the sensor to report a failure.
Frequent issues can also occur from simpler conditions, like different process levels between the vessel and the bypass chambers created due to manometric pressure in multiple fluids.
DENSITY PROFILING
This brings us to a discussion on the possible solutions for measurements with large emulsion layers. In applications like desalters, dehydrators and separators; emulsions can form due to poor separation between oil and water.
Furthermore, other layers like sand and foam create different density gradients within the process, which demands a more sophisticated instrument for measurement.
To tackle this tough demand, a Multiple-Point Density Array (MDA) can measure the densities at each known elevation. This way the operator can control not just the water level, but also the emulsion band and sand levels.
A density profiler is designed around radiometric measurement due to the level of detail it can provide around density measurement. If sized well, density resolutions as low as +/-2mm can be achieved. This will help operations to identify the smallest difference between oil, emulsions and water.
The need for the high density resolution cannot be understated, since the density span between oil and water is normally 150 kg per cu m. Offering a poor density resolution like 30 kg per cu m or worse is pointless in differentiating the different gradients is such a narrow span. With heavier crudes, the density gradients become even tighter where no measurement is possible without such high resolutions provided by a fixed gauge density profiler.
The need to understand emulsions and further reduce its presence in the process has been more of a demand now. If the emulsions are not detected, water particles can reach the electrostatic grids that is used to improve desalting and damage it.
Emulsions also contain cashable crude which can be lost with the water drained from the bottom of these vessels. Hence, measuring the interface level and the emulsion band has become more critical to improve profitability.
Further, measuring the emulsion band will help reduce chemical costs drastically. Demulsifying chemicals are added to reduce the emulsions which are measured traditionally by manually checking the samples from valves. Dosing effectively these expensive chemicals is a real challenge when the exact emulsion thickness remains unknown. This can lead to unnecessary wastage, thus driving up costs for oil and gas companies.
Not all interface level measurements, which look challenging needs an elaborate measurement like a multiple density array. Even though the installation looks challenging, simpler solutions can be employed.
Such is the case for crude oil and refined product storage tanks. These huge storage tanks has water settling at the bottom, which has to be dewatered. In such tall tanks, the difficulty constructing tapping points for a differential pressure transmitters or bypass chamber connections at the very bottom of these tanks, provides no way to measure the water level.
Normally oil or water detection meters are deployed on the outlet pipe, but the measurement is active only after the oil reaches a certain point in the pipe. Measuring the interface level in the tank would be better for a more efficient control.
This measurement can be easily done with a top mounted differential pressure transmitter, which can be deployed without any tank modification, using the electronic differential technology.
A suspended hydrostatic level measurements is not commonly employed the oil and gas industry. But due to the flexibility in installation, the interface level in dewatering tanks can be easily solved by dropping in two hydrostatic sensors and measuring the interface using electronic differential, which makes the system easy to use with minimal maintenance.