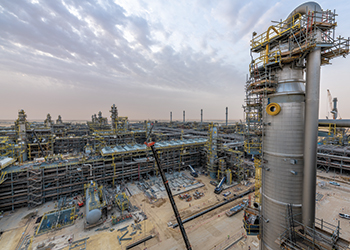
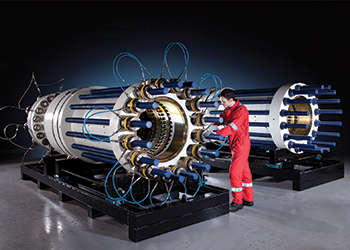
Maintaining a current understanding of the technology available within the industry is an important part in maintaining a fit-for-purpose Emergency Pipeline Repair System, James Rowley, Business Development Director, Connector Subsea Solutions, tells OGN
An Emergency Pipeline Repair System (EPRS) is, in its simplest form, a contingency plan in case an onshore or offshore pipeline asset is damaged. These systems have existed for over 30 years and have taken the form of a paper risk assessment right through to fully built systems stored in contingency and located in-country, close to the assets.
In recent years this has become a hot topic as operators have been investigating exactly how suitable their plan is for today’s current economic and political climate. Nowhere is this truer than in the Middle East where 65 per cent of Opec oil reserves (which forms nearly 80 per cent of the worlds proven oil reserves) are located and transported, often through aging, large bore pipelines.
RATING RISK
To justify the time, effort and cost of an EPRS, the pipeline asset owner must first understand the risk. The simple formula of ‘probability (of pipeline damage) x cost (of repair) = risk’ rating is the easy approach. However, neither the probability of damage nor the cost of repair is a stationary value.
![]() |
CSS EPRS storage |
Every pipeline in the world is at risk of damage and, therefore, the probability will never be 0 per cent. Physical damage through impact (dropped objects, dragged anchors, collision) is always an uncertain risk. However, as assets age, they become more likely to fatigue or succumb to erosion or corrosion – the highest ranked contributor to pipeline failures.
The risk to pipelines that cross state boundaries can also be difficult to assess as they are subject to geo-political turmoil and can become a target, such as the drone attacks on September 14, 2019 where two Saudi Aramco plants were targeted and led to 5.7 million barrels per day of Saudi crude output being stopped.
The probability of risk to an individual pipeline will always be extremely low and typically an EPRS is only of real value when there are multiple pipeline assets to consider.
Even when the probability is low, the risk to the operator is a function of cost. Not simply the cost of repair equipment but the cost of mobilisation time, service costs, downtime, lost production, pollution and the damage to the company’s image, which can translate to investor confidence and share price.
The September 14 attack cut the equivalent to over 5 per cent of the world’s supply, but impact will ripple beyond simply lost production. These huge costs can quickly multiply further when assessing large diameter, high pressure or clad and lined pipelines.
Each operator and pipeline owner are responsible for understanding the risk rating to their assets and deciding what EPRS needs to be in place to mitigate that risk.
FUTURE CONSIDERATIONS
Maintaining a current understanding of the technology available within the industry is an important part in maintaining a fit-for-purpose EPRS.
![]() |
The world’s first DNVGL type approved connector |
In the last 12-months alone, the world’s first diver-less remote hyperbaric tie-in operation took place in Norway and the world’s first DNV type approved mechanical connector for the permanent repair of clad and lined pipes was launched. Digitisation, automatic systems and advanced monitoring are being developed and implemented.
Although the ongoing global pandemic has taught many individuals and businesses that with the latest digital technology, remote information access and working is both feasible and practical, the need for technical and service support local to the asset is still very much required.
As each pipeline is subject to specific circumstances unique to the geography, location and pipe media, so also can each repair be made bespoke to provide the highest level of performance and quality within the boundaries of project delivery, location, schedule and budget. The way the repair solutions are packaged into an EPRS that is specifically designed to suit the requirements of an operator can likewise be tailored.
As an industry we have never been so well connected to ensure the traditional philosophies of safety and integrity can be implemented with the new technologies and advancements that are achieved in the worlds harshest environments.
* An EPRS provider and owner of Morgrip Clamp and Connector product lines, Connector Subsea Solutions champions pipeline repair solutions that are based on core design philosophy of promoting lightweight, reliable and innovative permanent solutions.