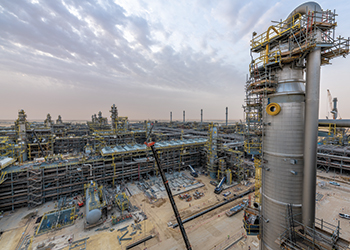
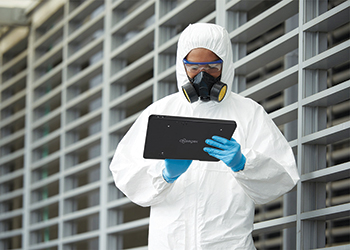
Industry 4.0, IoT, Cloud, Advanced Analytics and Machine Learning are all changing the landscape of process manufacturing and industrial machine maintenance. While there is much buzz around these ideas, implementation in real-world manufacturing applications can be complicated, challenging, and costly to implement.
Aegex Technologies offers a complete and cost-effective Industry 4.0 solution for those industries that operate in hazardous, potentially explosive environments found in oil and gas production and chemical process plants. "Properly equipping the company’s most valuable resource, that is people, is the first step in improving efficiency and informing the entire operation about the health of the business," Thomas Ventulett, CEO Aegex Technologies, tells OGN.
Aegex recently worked with a facility whose manufacturing process can result in a significant noxious gas as the result of production. Failure to contain and mitigate this odour can result in permits revoked, and potential liability of inhalation claims from surrounding facilities and residential areas.
Additionally, many of the constituent gases in a high concentration can become volatile, requiring all sensing equipment to be intrinsically safe.
The smell itself is the result of several gasses mixing to create the noxious aroma and called for a very creative solution to monitor and identify the gasses as well as predict potential plume direction to contain the output within the company’s property.
Utilising the aegex10 Intrinsically Safe tablet, engineers were able to inspect pumps, valves, and other machinery in Zone 1 areas of the facility, while providing photos of potential problem areas via the cloud to engineers working remotely.
The ability to immediately document the completion of equipment inspections and maintenance checks verified with the time and location of the work has improved the performance and accountability of tasks conducted by contractors.
By providing field access to drawings, maintenance records, or manuals, field personnel complete tasks faster and more efficiently, freeing up time to address more challenging fugitive emissions problems and, ultimately, reducing costs and improving operational performance and safety.
With a working knowledge of the facility’s areas of concern identified, Aegex worked closely with company engineers to deploy a system of five Aegex NexVu Endpoints that wirelessly monitor simultaneously O2, CO2, CO, O3, CH4, CH4S, SO2, NH3, and H2S, as well as an intrinsically safe weather station and vibration sensors.
From the first call with the customer to fully operational, Aegex implemented the entire system in just three weeks. Aegex’s novel and innovative design enabled the installation of 60 unique intrinsically safe sensors in only two days.
Gas sensors placed in various locations near the probable source of the odour were able to measure the rise and fall of the constituent gases until establishing a unique ‘digital signature’ of the offensive smell while ensuring that hazardous conditions did not arise.
Given the unique combination of potential gases present, special consideration was given to the placement of sensors to measure both those gases that rise versus fall in the atmosphere.
The data feed is real-time to the Azure Cloud for data collection and analytics. The NexVu system updated field staff with evolving notifications when the presence of gas rose in the production facility.
To ensure air scrubbers were filtering the air properly on the exterior of the facility, additional endpoints were placed at the discharge point to measure output. If the odour is detected outside the facility, a third-tier critical alarm occurs, alerting monitors and assessing formation of a gas plume and its projected movement off property.
As alarm conditions occur, connected field workers with tablets receive an immediate notification, with remediation or mitigation actions identified to ensure operations remain productive and safe.
Lastly, the overall solution has provided the customer with an ability to conduct operational assessments to identify and evaluate other potential risks such as pump failures or areas of improvement.
NexVu’s modular design, coupled with its swift installation, affordability, and flexible design, enabled full fence line monitoring of fugitive gases in weeks.
Combined with the Aegex tablet and the Azure Microsoft Cloud, the system immediately provided the client’s staff with real-time analytics and predictive actions averting costly risks to their operations.