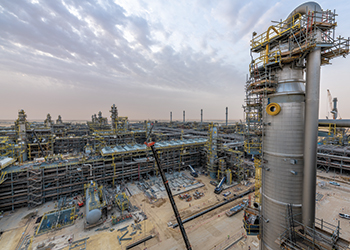
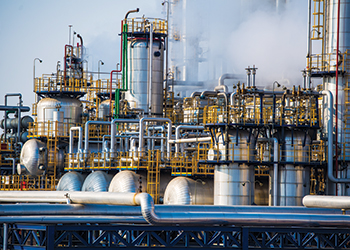
It’s been estimated that over 80 per cent of projects in oil and gas are over budget and/or exceed schedules. Throw in a global pandemic and a turbulent oil price scenario, and the outlook for delivering on time and on budget becomes ever more challenging.
So, what role can suppliers take to improve the hit rate?
According to Ian Rowell, Segment Manager Protective Coatings for AkzoNobel, one of the first steps is to get suppliers in a project integrated as early as possible to ensure that designs are optimised and materials, such as coatings and fire protection, can be designed into the structure in question.
He says: 'Coatings account for less than 0.5 per cent of the budget on a project but are used on up to 98 per cent of the surfaces in question, indicating a real opportunity to design in better solutions for cost and scheduling, both offsite and onsite.'
Two of the best opportunities for early integration optimisation come in the form of passive fire protection (PFP) and universal pipe coatings.
PFP has historically been specified using a prescriptive approach of one size fits all – one failure temperature, one material thickness, one solution – but more recently a drive to optimise designs through a multi-sectional approach is gaining popularity. This approach considers steel utilisation, loads and different steel shapes to indicate a thickness of material to be used on each beam or column type.
This approach assures an optimised design, reduced material usage and reduced structure weight. When combined with a product, which can be applied in a single coat, mesh free, you get a solution which is lighter, cheaper and can save time during application, helping to meet schedules. On a typical 100,000 sq m job, this approach can reduce both material usage and application time by around 30 per cent.
In addition, like most materials over time, PFP applied to an asset in service comes under varying levels of stress resulting in a number of defects. Incorporating a detailed condition survey can highlight problem areas, comparing defects with tested and approved data, and recommending proper repair methods, allowing to eliminate uncertainty through reliable, predictable performance and easier, more cost-effective maintenance.
A 2018 report from Marsh Insurance indicated that over 30 per cent of failures on downstream facilities can be traced back to corrosion, with much of it being found on equipment that is under insulation. Damage caused by corrosion under insulation (CUI) and cyclic high temperatures is a common and ongoing threat to asset integrity in oil and gas facilities.
Moisture ingress into conventional insulation materials usually results in accelerated corrosion of the underlying steel surface, which, if left unchecked, can result in structural failure of the pipe, vessel or other insulated items.
Coatings solutions for high heat pipes, valves and other equipment has traditionally involved many products from several different suppliers. Combine this risk with this complexity and productivity, performance and cost will all be impacted – all key elements of asset integrity management.
Operational conditions on pipes, valves and vessels cover the temperature range from -196 deg C to 650 deg C, but instead of a vast array of products, it is possible to use a three-product solution to cover both new construction and maintenance operations. This three-product solution should include an alkylated amine epoxy for fabrication and maintenance use to 230 deg C, a universal pipe coating covering the full temperature range and a hot spread solution for application to in-service hot equipment. Sourcing this three-product solution from one supplier can provide peace of mind and reduce cost and complexity.
Manufacturing in Dammam since 1983, AkzoNobel Saudi Arabia is a joint venture partnership with Yusuf Bin Ahmed Kanoo. Products meeting these standards can be manufactured in Dammam by AkzoNobel helping with local content requirements.
AkzoNobel has invested over €2 million ($2.37 million) to become the only in-country manufacturer of epoxy passive fire protection. Over 31 per cent of employees in KSA are Saudi nationals and an IKTVA score of 25 was achieved in 2019, far above the benchmark for coatings manufacturers of 10.